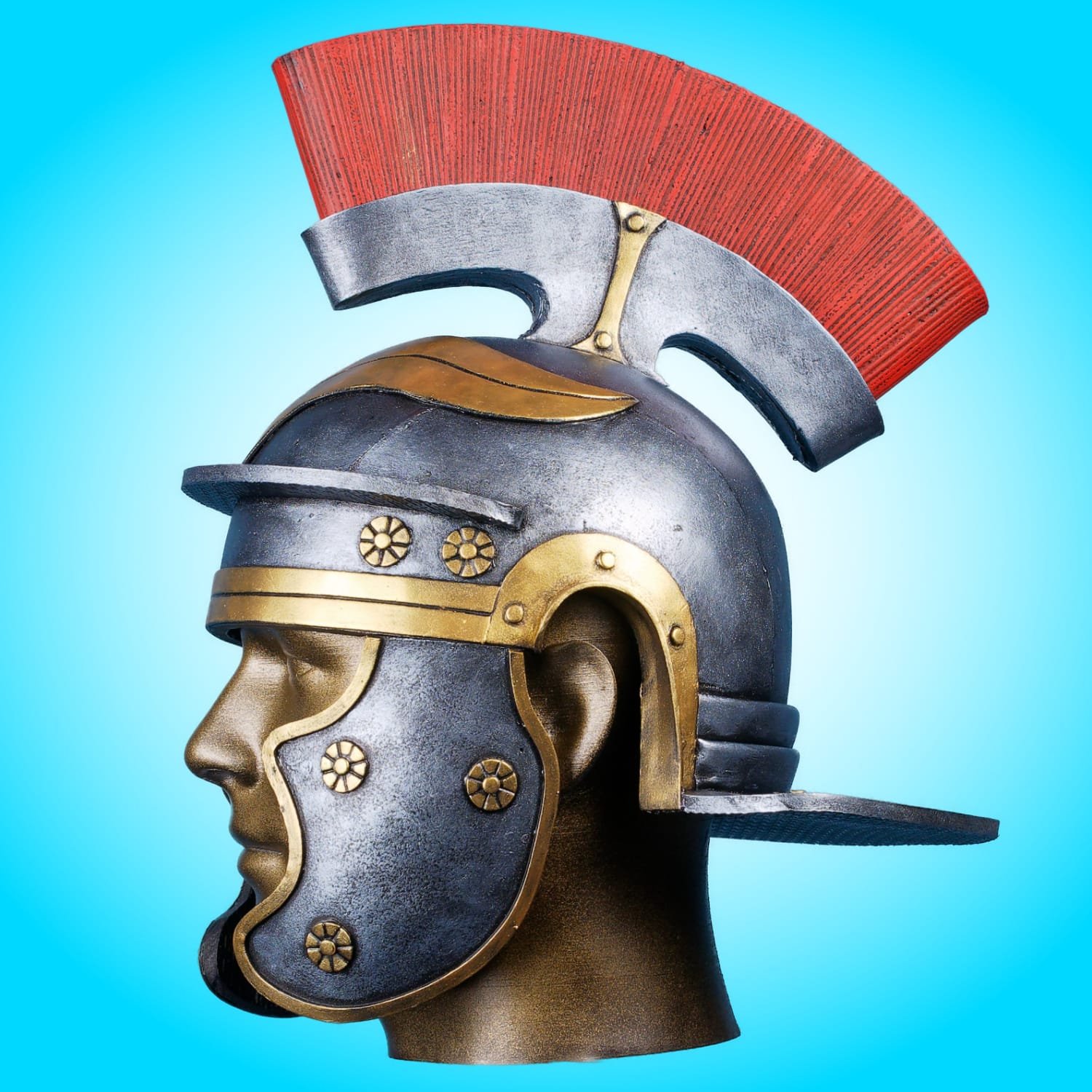
DIY Roman Centurion Helmet Made From Foam!
How to make a Roman helmet from a foam floormat- pattern and tutorial

DIY Ninja Turtle Shell From a Foam Mat!
Make your own turtle shell in an evening with this pattern and tutorial!
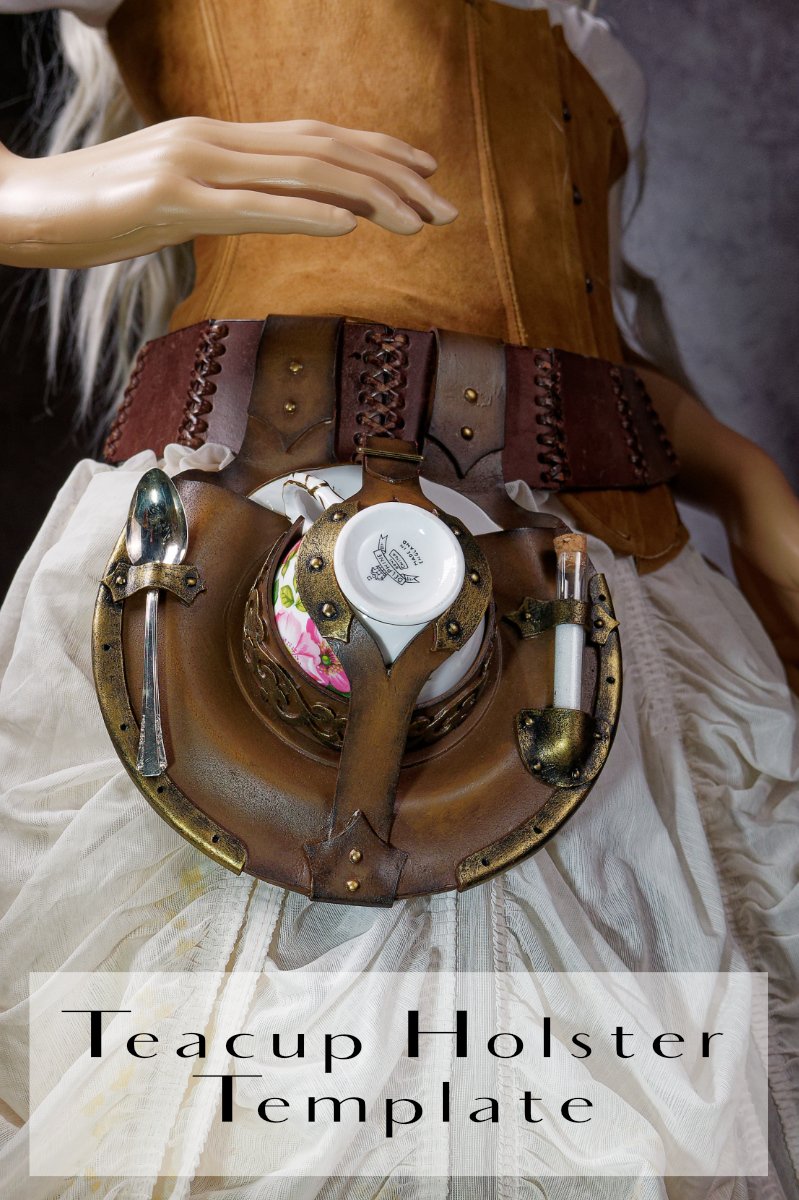
DIY Steampunk Teacup Holster. Template and Tutorial
It’s the little things that make the difference. Try upping your steampunk costume game with this handy little teacup holster you can make yourself in an afternoon!
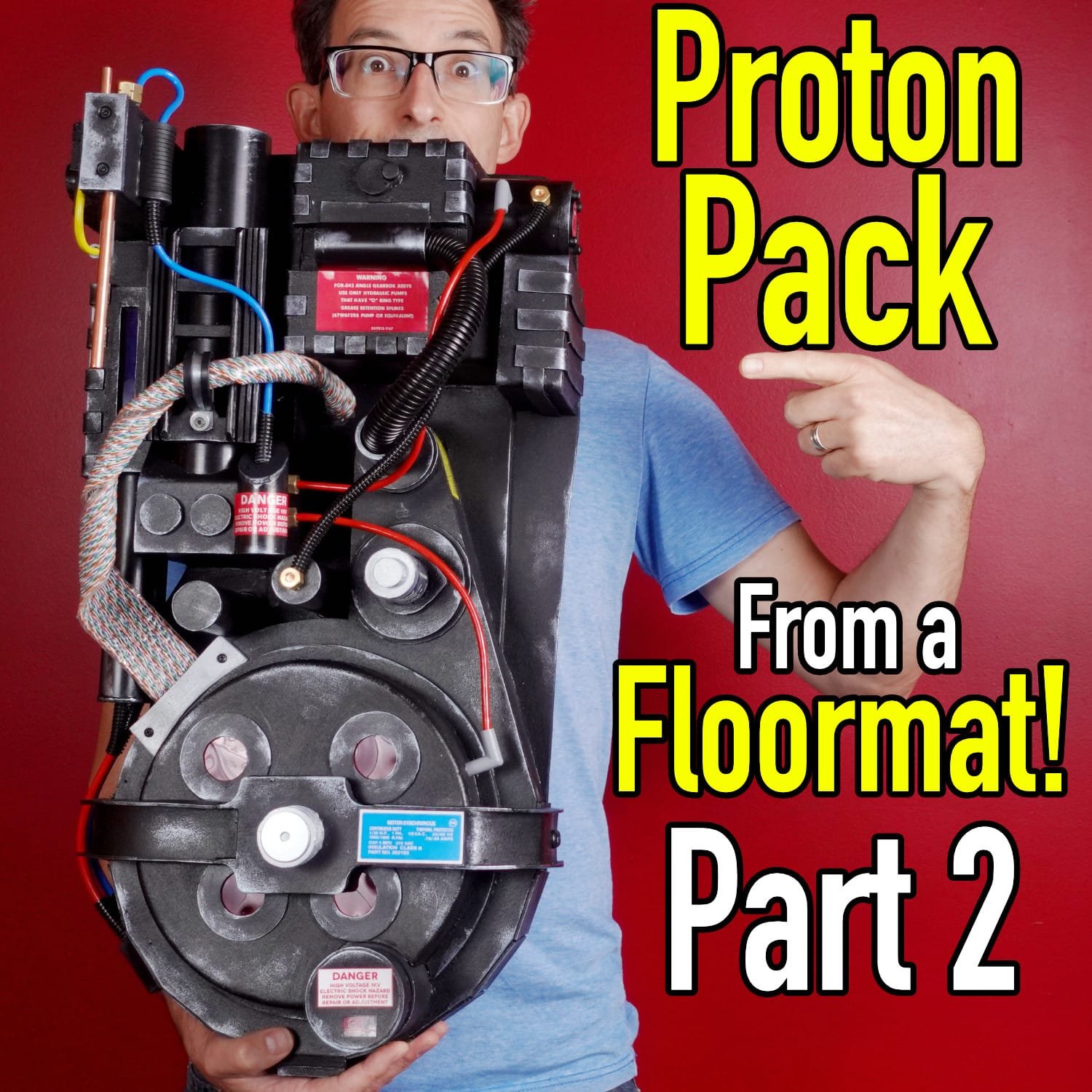
DIY Ghostbusters Proton Pack Template
Ghosts. Nobody wants them, and there’s only one way to catch them. With an unlicensed nuclear accelerator strapped to your back, of course. Enter the Proton Pack.
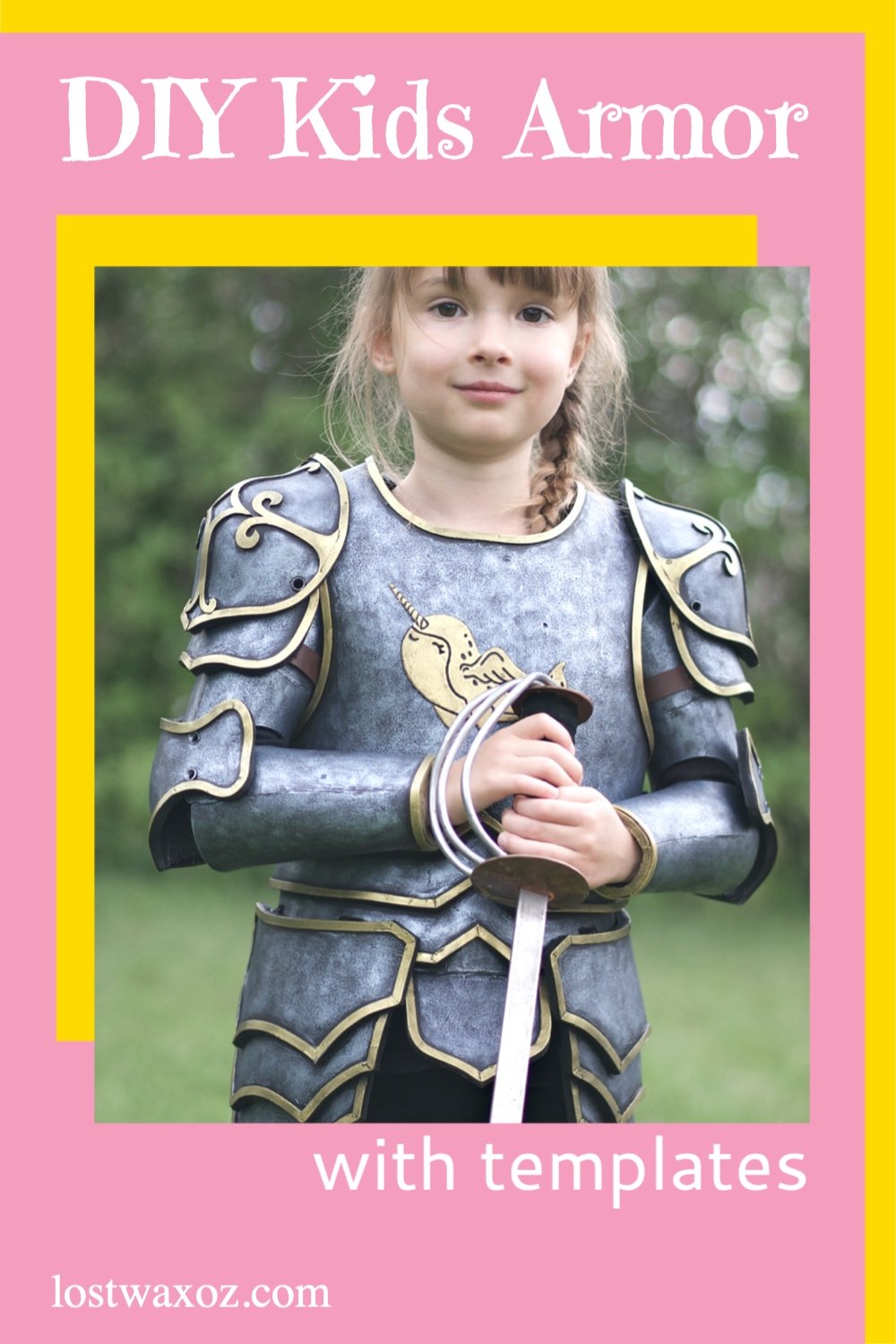
Kids Knight Armor Pattern is Here!
I recently made some epic knight armor, complete with pattern and DIY video. And today I’m happy to say I’ve expanded the pattern to also include child-sized knight armor! The basic build is…
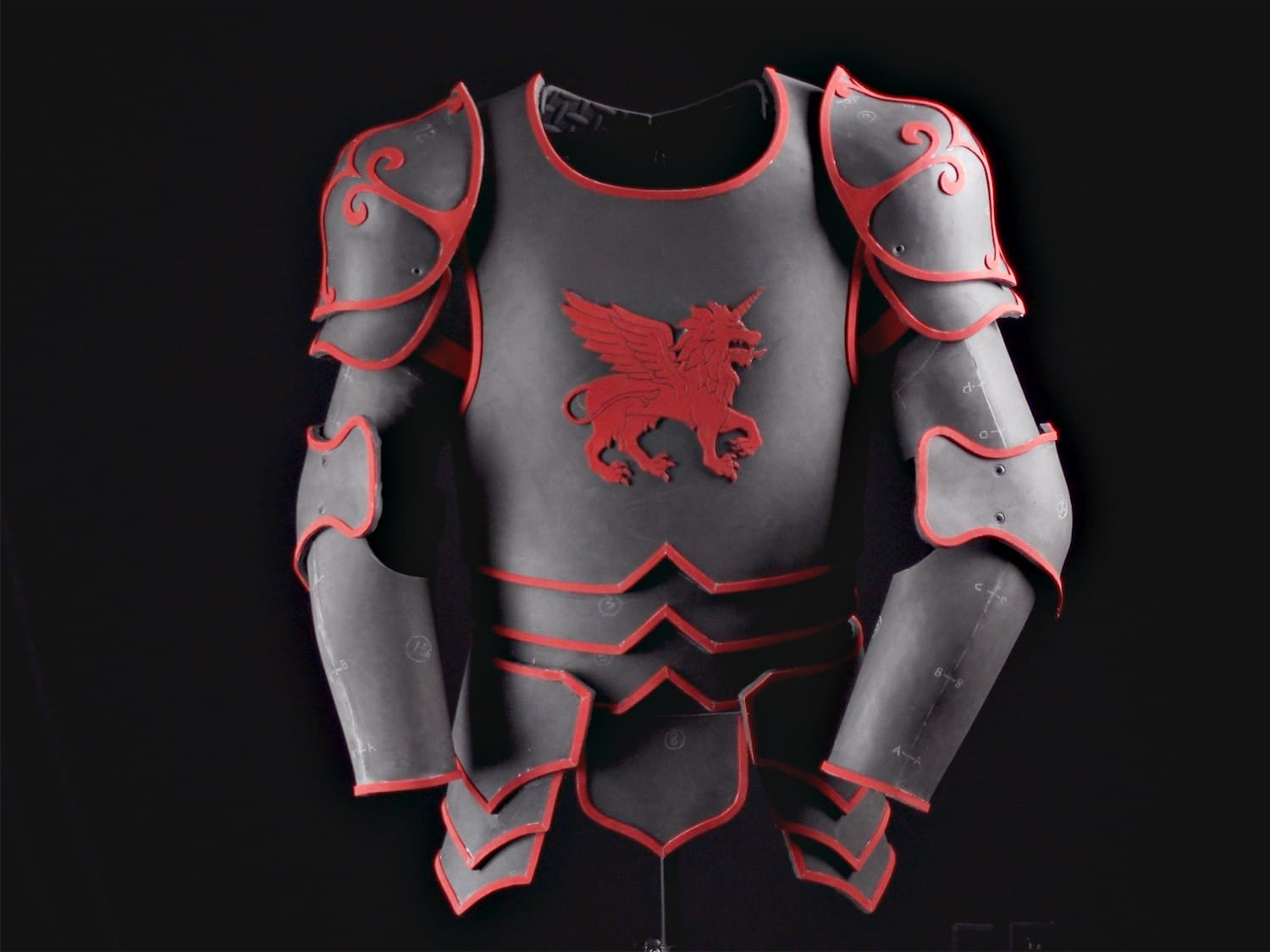
How to Make Knight Armor ...From Foam
Years ago, I made a Halloween knight costume for my son and have since had a lot of requests for the pattern. I made the knight helmet pattern but…